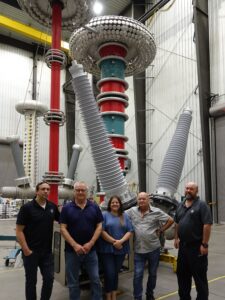
June 9th is World Accreditation Day, a day established by IAF and ILAC to recognize the importance of accreditation, a formal recognition earned by organizations proving they are qualified, competent, and comply with international standards. Not only does accreditation create confidence in the safety and quality of products and services we use every day, but also effectively manages organizational risk, reduces barriers for global trade, and much more.
This year’s theme for World Accreditation Day is “Accreditation: Empowering Tomorrow and Shaping the Future,” which places a fundamental focus on sustainability, digitalization, new technologies, and other environmental concerns. As the world around us rapidly evolves, accreditation is the foundation for maintaining competence and quality in just about every industry, all around the world.
The IAF and ILAC Joint Statement regarding World Accreditation Day 2024 reads, “By providing a framework of trust and reliability, accreditation enables organizations to confidently embrace new technologies and drive innovation.”
To explore this year’s World Accreditation Day theme, A2LA Director of Government Relations Randy Querry sat down with our customers and friends at GE Grid Solutions Research and Development (R&D) Testing Lab. They discussed how accreditation has supported their organization as they continue to meet their customers swiftly changing demands amongst the implementation of renewable energy, the effects of climate change, and much more.
The GE Grid Solutions R&D Test Lab is ISO 17025: 2017 accredited in the electrical field of testing and has been accredited with A2LA since 2010. They serve a variety of customers including utilities, various engineering companies, and different government entities.
Here’s what they had to say:
RQ: Randy Querry, Director of Government Relations
JR: Justin Rebovich, Sr. Lead Test Engineer
VH: Victor Hermosillo, Principal Engineer
MS: Matthias Schirmer, Product Development Manager
TT: Thomas Tometich, Lead Test Engineer
RQ: Can you tell me a little bit about your organization and the work you do?
JR: GE Grid Solutions R&D Testing Lab is a 15,000 sq ft area within our 175,000 sq ft production facility with three full time staff members including myself (Sr. Lead Test Engineer Justin Rebovich) and Lead Test Engineer Thomas Tometich and Test Technician Brian Shimko. We are also supported by Product Development Manager Matthias Schirmer, Principal Engineer Victor Hermosillo, and Technical Writer Lindsey Walton.
Our team’s primary day-to-day focus is new design verification and product development testing for high voltage dead tank circuit breakers. We also assist in quality control activities for the production side of the organization, and sometimes conduct tests for customers in our facility.
RQ: How long has GE Grid Solutions been providing solutions for the grid?
JR: Our facility in Charleroi, PA has existed since 1994 and we’ve gone through multiple expansions over those nearly thirty years.
RQ: Has it been challenging integrating renewable energy sources to the grid?
JR: The challenge is the sheer amount of equipment being ordered across the industry for integration for renewable energy as well as replacement of existing equipment. Those new equipment requests often involve higher ratings, which ultimately leads to product extensions or new products.
RQ: How has climate change, like notably stronger storms or extreme temperatures, impacted grid resilience? Has GE Grid Solutions aided in this?
JR: Our goal is to fulfill customer orders so that the end user can strengthen their section of the grid. We need to supply our customers with equipment that is more resilient and has higher performance capabilities.
VH: With renewables, the demand for the equipment is increasing and every customer has their own requirements. They require more customizations and there are about 2,000 different specifications in the U.S. These requirements are reflected in the types of tests we do. For example, some equipment will be used at extreme altitudes or extreme environmental conditions, so we need to test hotter temperatures or colder temperatures in our environmental chamber, etc.
RQ: How has your organization changed in the past 5 years? How do you think it will change in the future?
JR: Due to customer demand for this equipment, it has led to faster development time. The time to market needs to be shorter. Everyone wants new, more capable equipment, and they want it faster.
RQ: What led your laboratory to seek accreditation, and what value has accreditation brought to your organization?
JR: We sought accreditation to increase customer confidence in our test results. It also further reinforces the capabilities of our products. Seeing the A2LA accredited symbol on our reports, customers are beginning to understand the effort that goes into the accreditation and what it means for the results obtained for a particular piece of equipment.
TT: It gives them confidence that the equipment can do what we say it can do.
VH: And, if you look at the international market, most international customers will not accept reports if they’re not from an accredited lab. Something we saw in the past before accreditation was that we’d need to repeat a test again with an accredited lab, even though we had already completed the test.
JR: Either that, or the customer would send a representative to witness the test firsthand. Accreditation has helped do away with a lot of those extra steps. They’re already confident in the results we provide.
RQ: Do you work with international customers?
MS: We have a variety of international customers. Over the years it has changed depending on the volumes in the US market, but we still have international customers that rely on us in places like the United Kingdom, Australia, and Canada.
JR: Believe it or not, one of the first things we consider when we want to design a new breaker is how we are going to ship it, whether its domestic or international. We have to have a plan or an idea, and the design is tailored toward our capabilities for shipping it wherever it needs to go.
VH: Accreditation has also allowed us to become members of Short-Circuit Testing Liaison of the Nations of the Americas (STLNA), a chapter of a well-known global group for high-voltage testing labs. Members must be accredited to be part of the organization.
RQ: What is something that the US energy consumer does not realize and takes for granted every time they plug into the grid?
JR: The short answer is—everything! Most people don’t know what it takes to get power to their house or place of business. There’s an enormous amount of people that dedicate their entire careers to this industry. Each generation is building on the knowledge of the prior. We only work on a very small piece of the power grid, the circuit breaker. There are people who work with transformers, there’s people who work with power generation and many more devices that are essential to the power grid; all these people are working behind the scenes to keep the lights on every single day.
RQ: From your perspective, how can we be better consumers of electricity?
JR: Conserve it. Don’t waste it. That’s a broad statement to make but that’s my answer!
For more information about earning accreditation for your organization, reach out to A2LA at info@A2LA.org.